The pressure-delay compound is brought into the roll gap under the rotating friction of the surface of the roll, and is subjected to extrusion and shearing, and plastic flow deformation occurs. However, the position of the rubber on the roller is different, and the magnitude of the pressing force and the flow velocity distribution are different. There is a causal relationship between the pressure change and the flow velocity distribution.
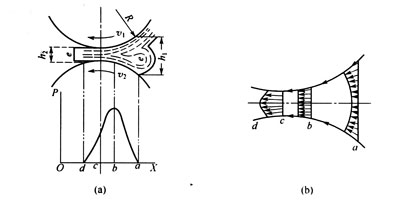
At ab, at the pressure starting point a of the rubber compound, the rubber material is subjected to a small pressing force, so that the flow rate of the rubber at the center of the cross-section is small, and the flow velocity at the two sides of the roller near the surface of the roller is small. As the rubber advances, the roller distance gradually decreases, and the pressure applied to the rubber material gradually increases, so that the flow velocity at the center of the cross section gradually increases, and the flow velocity on both sides does not change. When the point b is reached, the flow velocity at the center and both sides tends to be the same. At this time, the rubber material is subjected to a maximum pressing force. As the compound continues to advance, although the applied compressive force begins to decrease, the flow rate of the compound at the center of the section is accelerated by the continued decrease in the interpupillary distance.
Since the flow rates on both sides are constant, when reaching the center point e of the cylinder section, the flow velocity at the center of the section is already greater than the flow velocity on both sides. After the point c, the pressure and flow rate are gradually reduced due to the gradual increase of the nip. The pressure at the point d reaches zero and the flow rate tends to be consistent. At this time, the rubber has left the nip and its thickness is also increased by a certain amount at c.
During the calendering process, the rubber has a radial reaction force on the surface of the roll, called transverse pressure. In general, as the viscosity of the compound increases, the rolling speed increases, the roll temperature decreases, the amount of glue supplied increases, and the width and thickness of the semi-finished product increase, the transverse pressure of the rubber to the roll also increases.