The dipping process of the cotton cord includes the steps of guiding, dipping, extruding, drying and winding of the cord. After the curtain is opened, it is adjusted by the joint and the storage cloth and then enters the dipping liquid. When the dipping liquid is left after contact for a certain period of time, the inside and the surface of the cord structure are filled with a layer of latex-resin polymer layer, and then extruded. The roller squeeze removes most of the moisture and excess adhesive, and then enters the drying chamber to dry, so that the water content is reduced to the specified limit, and the expansion roll is expanded and rolled up or directly sent to the calender for laminating. A uniform and constant tension of a certain size must be applied to the cord during the dipping process to prevent the cord from shrinking.
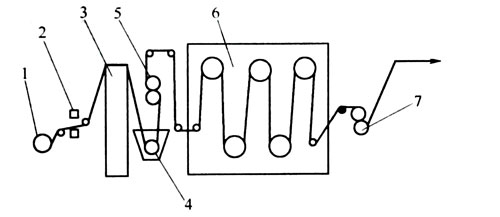
The concentration of the dipping solution, the time the fabric is in contact with the glue, the amount of the glue, the pressing force of the cord, the magnitude and uniformity of the stretching force, and the degree of drying all affect the quality of the dipped rubber cord.
Cotton, rayon, vinylon and nylon cords can be immersed in RFI only once. Polyester, aramid and glass fiber cords must be surface modified and then impregnated with RFL to ensure the quality of the tape.
The glass fiber must be impregnated with a treatment liquid consisting of 20 parts of a water-soluble varnish and a silane coupling agent of 0.6 to 1.0 parts in the drawing process before being subjected to dipping (RFL). The dipping time is 6~8s, the drying condition after dipping is 170°CX (1~2)min, the amount of glue is 18%~30%, and the dipping should be fully saturated, so that the surface of each monofilament is coated. A complete polymer film is preferably treated by two RFL liquid immersion treatments.